無論是再生能源、電動交通還是節(jié)能,電力電子正變得越來越重要。為了進軍這些市場,創(chuàng)新是必要的,因為不同的市場有不同的需求,這些需求所要求的解決方案超出了20世紀90年代所廣泛接受的工業(yè)標準。
賽米控是一個創(chuàng)新者,不斷沿著新路徑探索。導(dǎo)熱硅脂和綁定線是工業(yè)模塊中奄奄一息的“殘余”,現(xiàn)在正被高度可靠的燒結(jié)層和用于指定應(yīng)用的柔性板所取代。
全球?qū)Νh(huán)境政策的新關(guān)注和選擇能源時消費行為中不斷增長的環(huán)保意識使得電力電子作為一種能量轉(zhuǎn)換和控制的可能手段更加具有意義。產(chǎn)品和應(yīng)用在效率、可靠性和大小方面正被優(yōu)化。電力電子有助于未來基于混合動力技術(shù)和電動汽車的交通發(fā)展,并在減少日益增長的排放和不斷減少的資源中扮演關(guān)鍵的角色。為了滿足這些市場的需求和改善普遍接受程度,電力電子領(lǐng)域的新發(fā)展是必不可少的。在這方面特別重要的是提高可靠性的同時實現(xiàn)更高的功率密度,減小體積。電力電子設(shè)備制造商都面臨著滿足這些相互矛盾的要求的挑戰(zhàn)。更有甚者,功率也要增加,這意味著諸如并聯(lián)和熱管理也將承擔更多的重要性。未來的電力電子技術(shù)將在快速增長的可再生能源市場以及電動汽車市場這兩方面受益。首先,發(fā)電過程中的能量轉(zhuǎn)換需要功率半導(dǎo)體,例如風電變流器。其次,功率半導(dǎo)體是變速變流器的基本要素,這意味著它們是高效利用能源的關(guān)鍵。
可靠且低成本
在電動車輛中,電力電子器件必須節(jié)省空間、重量輕、并且即使在惡劣的條件下也要工作可靠。為了滿足這些要求,賽米控早已擯棄傳統(tǒng)基于模塊的方式,目前盡可能從機械方面集成電力電子系統(tǒng)所有的功能。圖1顯示了最新用于叉車的賽米控系統(tǒng)。開發(fā)中所面臨的挑戰(zhàn)實際上在于,相互矛盾的電氣、機械和散熱要求都必須滿足,同時實現(xiàn)最高的可靠性和合理的成本。5.7升逆變器具有400 Aeff的峰值電流,160V電池電壓,適合直接安裝在車輛的驅(qū)動橋上。在這樣的安裝位置上,系統(tǒng)必須能夠在12g的振動和100g的機械沖擊下無損運行—— 在外部溫度為-40~+85°C的條件下運行20000小時。
圖1 用于叉車的SKAI系統(tǒng)
早在20年前,賽米控開發(fā)了第一個用于風力渦輪機的IGBT模塊。這些模塊采用創(chuàng)新的壓接技術(shù),集成了電源、驅(qū)動器和傳感器功能,滿足這種全新應(yīng)用領(lǐng)域在長期可靠性和功率密度方面的挑戰(zhàn)。如今,第三代SkiiP IPM正被廣泛使用。迄今為止已安裝超過80GW,約為全球風力發(fā)電總裝機容量的一半。
- 1
- 2
- 3
- 4
- 總4頁
http:www.mangadaku.com/news/2011-9/201192110318.html
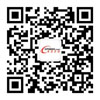
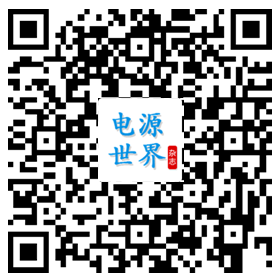